3D Printing
- pennarchtank
- Oct 9, 2018
- 4 min read
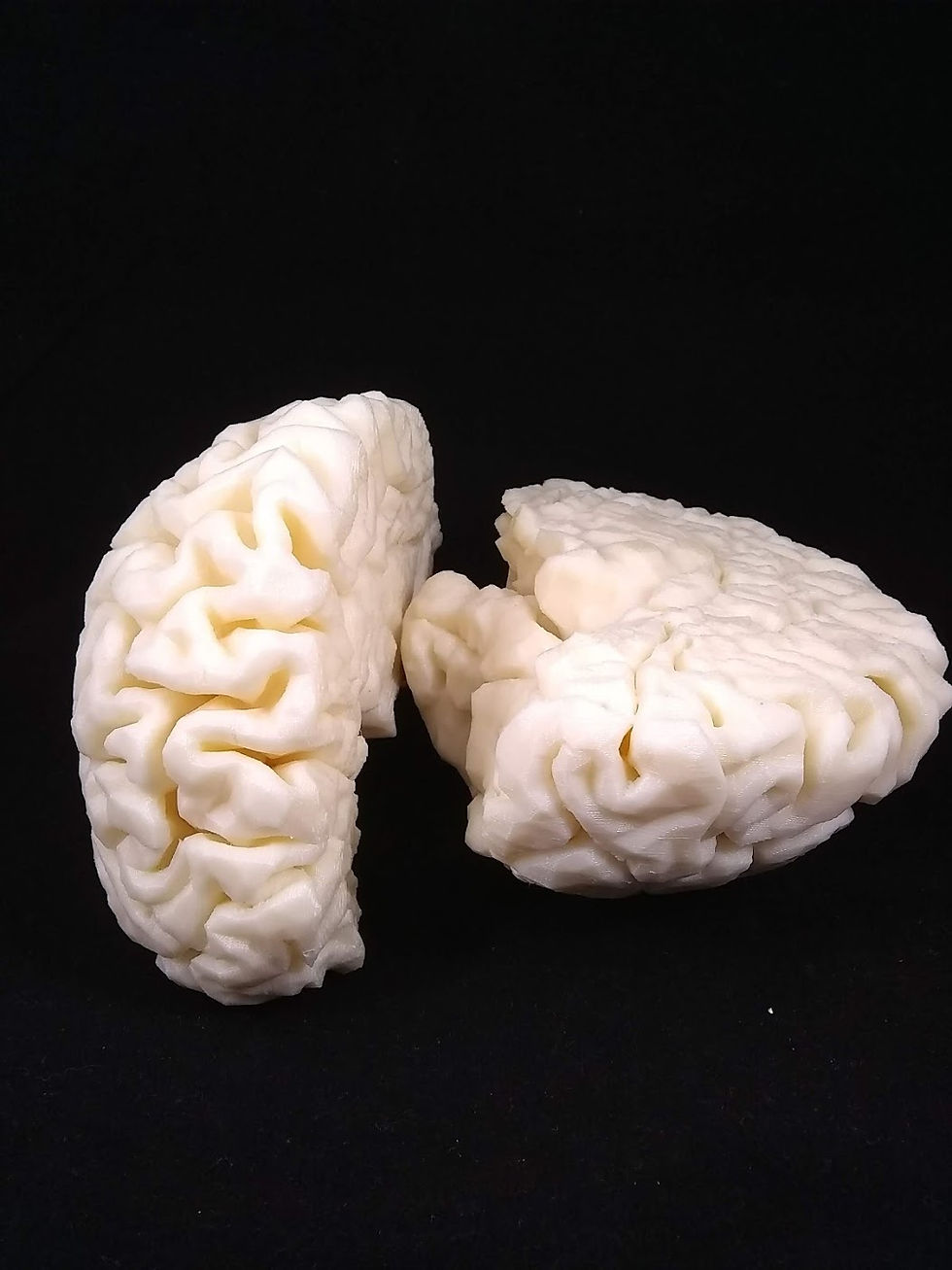
3D printing is an important part of visualizing architectural design. We believe that understanding the methods behind making your design is important to creating good design so this week’s post is part of a two part series on 3D printing. This week’s post is focused on different methods of 3D printing that you will experience at Penn and beyond. We’re going to go through some of the technology behind this amazing design tool and some of the places that you can access 3D printers around Penn’s campus. Next week’s post will include more information about how to make your designs 3D printable and work through a couple of big trouble shooting issues.
Two of the main manufacturing processes architects use are subtractive or additive – subtractive is when you take material away from a source to carve out the end result like CNC or laser cutting; additive is where you add successive layers to build up your final model as is the case in 3D modeling. Three of the main types of 3D printing you will encounter at Penn are FDM, SLS, and SLA.

Courtesy of 3D Hubs
FDM
FDM or Fusion Deposition Modeling is one of the most common methods of 3D printing available today. It uses an extruded to heat up plastic and place it in layers that create the physical shape of your model. Certain types of FDM printers allow you to use removable support to create pieces with complicated geometries and to print parts inside other pieces. FDM printers mainly use two kinds of plastic – ABS or PLA – to make their prints. ABS is a tougher industrial strength plastic that can withstand high heats and is very durable; however it tends to be significantly more expensive than PLA plastic. PLA plastic is a softer, cheaper option that is good for making quick prints or prototype models. The range of materials has expanded in recent years to include novelty products like a wood like material and specialty engineering materials that are flexible. One of the downsides of FDM printing is that the print is relatively weak in between the layers which means that they aren’t watertight and might break under high pressures at these points (they’re also NOT food safe because bacteria can get into the space between the layers and are almost impossible to get out).
SLS
SLS or Selective Laser Sintering uses a laser to melt powder together to create the 3D model. The model is built as thin layers of powder are laid down and successively melted; this method of powder layering creates a self supporting base for the model allowing more complicated structures and delicate features to be built than with FDM where external supports would need to be generated. SLS printing generally uses a type of powder material to create its models; in the FABLab at Penn you’re most likely to encounter a type of gypsum powder but certain specialty printers can also use a sort of metal powder to create metal prints.
SLA
SLA or Stereolithography is similar to SLS in that it uses a laser to selectively melt certain areas of a liquid resin material together to create a solid eventually building up the model over a series of layers. Depending on the brand of machine that you are using, some SLA printers build the model in a vat of resin so that it’s self supporting like SLS printers, but other brands build the model where the build plate sits upside down in a tank of resin and external supports need to be created to hold the model to the build plate. One of the advantages of using SLA is the wide variety of resins that you can use to build your model; generally the prints are made from a resin that hardens into something similar to plastic but there are also specialty engineering resins that mimic ABS plastic, flexible materials, high temperature materials, ceramics, and wax.
These are just some of the main types of 3D printing that you will experience at Penn for more in depth information about these methods and others check out these links here:
One of the biggest limiting factors of 3D printing is the amount of time that it takes to create the model. With current technologies, prints are generally limited to the mechanical speed of the process that is making it (the time that it takes to lay down a layer, add more powder, or for the material to adhere to itself). Certain companies have started to work on speeding up the process to varying degrees of success. One of the most well known examples of speedy 3D printing is Carbon M1’s work with Adidas to create custom shoes. As of right now the biggest downside of these technologies of the cost but there is hope for the future of 3D printing. Check out these links to find out more:
At the University of Pennsylvania we have a variety of printing services available to faculty and students. The printing service that architects are most likely to use is the FABLab in Meyerson. The specific services that the FABLab offers are FDM and SLS printing. You should keep in mind that during midterms or finals you are competing with all of the other design students at the university for a spot in the queue and due to the way that 3D printers work at the moment, prints tend to take a while to build (so things tend to get stressful). There are other services around the university such as the engineering ADDLab, Education Commons, and the Biomedical Library that offer 3D printing either for a fee or for free and you can always use an outside source such as 3D Hubs or Shapeways if you are really desperate.
For a list of Penn’s facilities see here:
For outside facilities see here:
Comments